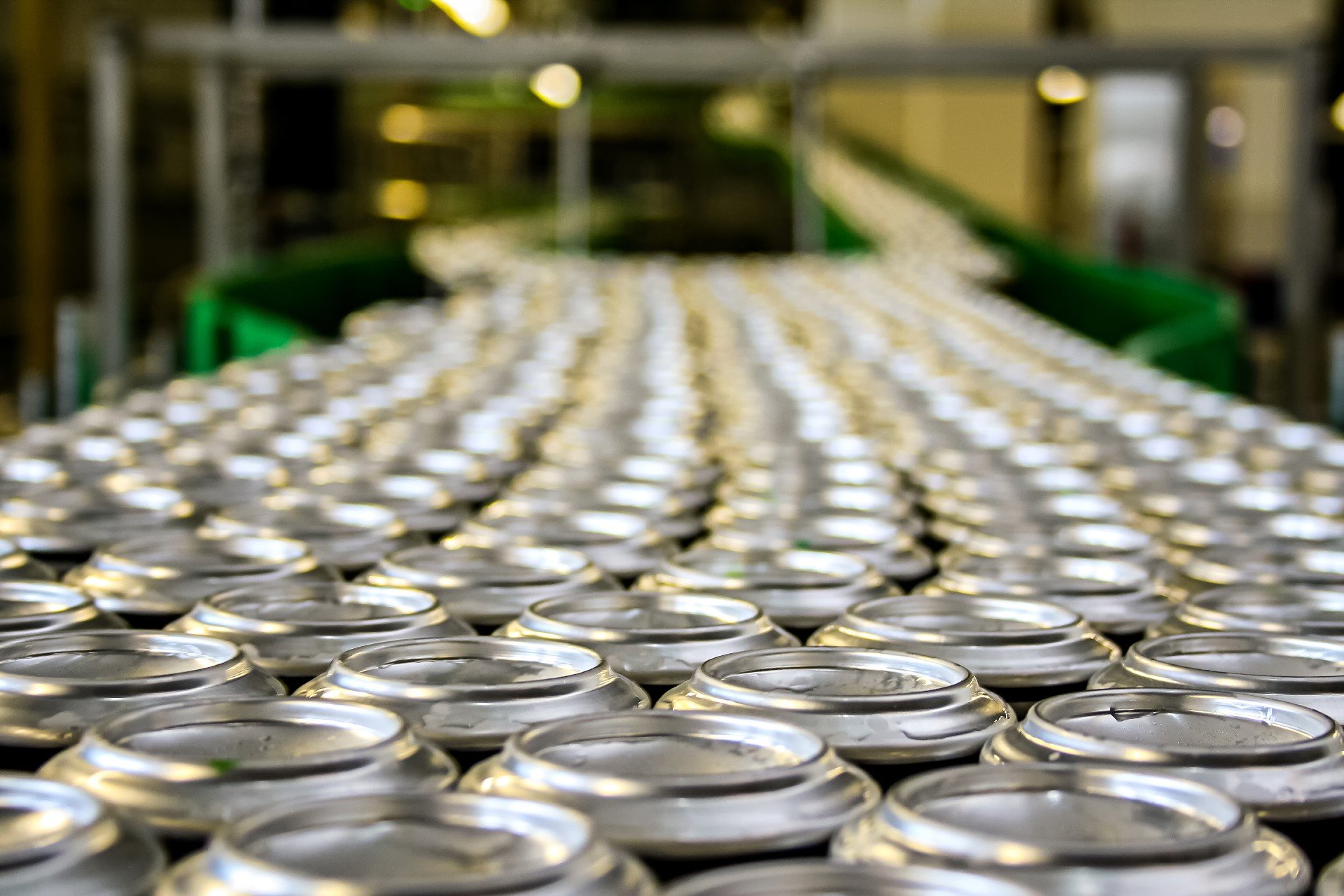
Diageo’s Road to AMIS success
Asset management is a key aspect of Diageo’s way of building manufacturing excellence and, by using AMIS, a vast improvement in plant performance, reliability and efficiency has been achieved at the company’s St Francis Abbey Brewery.
Over 300 years ago in 1710, John Smithwick began brewing his first ales. The Smithwick’s story actually started long before he chose the site of an ancient monastery, St Francis Abbey in Kilkenny City, to position his brewery, now a part of Diageo beer. Smithwick was inspired by a tradition of brewing on this site, the foundations which were laid back in the 13th century when the Franciscans established an Abbey, with its own well, on the banks of the River Nore in Kilkenny. While brewing and barley cultivation are recorded in Irish Annals from mists of time, the strong brewing tradition that exists in Kilkenny started with these monks who would have brewed light ale for their visitors, using water from St Francis’ well.
Diageo’s AMIS Journey
Far more recently, the engineering operations and management team of Diageo’s St Francis Abbey Brewery (SFAB) wanted to carry out an appraisal of management systems, methods, organisation and technology, it asked MCP to carry out its three-day AMIS Assessment. This assesses an organisation’s operations and asset management with the focus on driving improvements and benefits.
The Initial Assessment
The first audit involved representatives from maintenance, production and engineering working together to:
Determine plant performance improvements
Assess culture and motivational issues
Identify and agree on areas for improvement
Review the use of the CMMS, Spare parts management and Contractor Management
Develop a series of prioritised actions which will deliver business benefits
Diageo’s initial AMIS score was just 33%.
The Final Assessment
By following a four year AMIS Journey, with the engagement and wholehearted commitment of everyone on site, the asset management improvement plan helped them achieve an AMIS World-Class score of 80%. This placed the site in the top 3% of all 6,000 AMIS participating sites and at the top of all Irish participants. The score is well above the drinks sector average of 45%.
Robert Murphy, production manager, said:
“AMIS and the asset care journey have been key to the site’s overall improvement in plant and performance over the last four years. We have seen significant reductions in utility and site waste and costs through this journey. There has been full site engagement with involvement from engineering, production, laboratory and our contractor partners. This journey and the continued achievements by all in St Francis Abbey Brewery is something that we are very proud of.”
Asset management is a key aspect of Diageo’s way of building manufacturing excellence and by using AMIS, a huge increase in plant performance, reliability and efficiency were achieved.
How Does AMIS Work?
Sites audited by AMIS range from ‘chaos’ to ‘world-class.’ Key to improving a site’s status is moving from reactive to a planned maintenance culture. Such progress can be achieved through regular monitoring and improvement of a number of KPIs, including:
Adherence to plan: Weekly engineering planning meetings are held to prioritise workload and delegate resources, with daily meetings between shift managers, asset care technicians and engineering planners to ensure all work on the master-planned schedule is completed and for feedback reports. Technicians are required to record all their hours and tasks completed. This data is then compared against the master schedule in order to track the performance of craft and PPM strategy.
Planning effectiveness: In line with world-class standards, 80% of craft workers’ hours are allocated to conducting planned maintenance. Developing and implementing such a high level of planned maintenance requires cross-function planning and engagement from all areas of the site. Engagement has been critical to success.
Continuous improvement: In order to reduce costs and drive efficiencies, 15-20% of all recorded work by craft workers is aimed at continuous improvements (CI). The major improvement for Diageo was achieved despite major changes on-site and tight budgets and resources.
The Challenges
The following points summarise the main changes and challenges:
60% change in asset care technicians on a shift roster
30% change in operator asset care personnel
20% of employees left SFAB sites for roles in St. James’s Gate or externally
30% of employees changed to new roles internally within SFAB
Huge reduction in the maintenance budget
The Solution
A number of CI projects were implemented as a result of annual audits, these included:
Installation of swing sieve: The existing sieve in the brewhouse at the time was old and spare parts were not available. An asset care analysis highlighted that it generated a lot of waste and had a high associated cleaning cost. It was very time-consuming when craft intervention was required. This was replaced with a new swing sieve which was easily cleaned, required little operator/craft intervention and spare parts were readily available. This resulted in a huge reduction in downtime and greater reliability.
Tanker station software upgrade: Obsolete software at the tanker station was replaced with standard Siemens software. This allowed the engineering department to have greater input into plant modifications and improvement initiatives. This ultimately resulted in a reduction in beer waste.
Boiler control was modified to a software-based system which led to greater efficiency and reduced running costs.
An analysis was carried out on the plant which identified a critical control path for production. Based on this, duty standbys were installed for the whirlpool and wort stripper pumps meaning that production would not be interrupted and stalled due to any failure of these pumps in the future. This has resulted in a decrease in downtime.
An SAP analysis was conducted which highlighted certain pieces of equipment which were requiring maintenance interventions. The hot and cold liquor pumps in the brewhouse were identified as such and replaced with new pumps. These contained more efficient motors and seals which were easier to replace.
The Results
The site finally broke into the world-class zone after 3 years with an AMIS score of 75%, thereby placing it in the top 5% of AMIS participants. By the following year the AMIS audit showed continued improvement with a score of 80%, firmly consolidating the company’s position in the world-class AMIS zone.
The advantages and benefits of the AMIS Journey have reached all areas of operation at the site:
Health and safety: The site has now achieved over 670 days without a lost-time accident. This has been aided by site-wide engagement with AMIS. All site SIRs are now inputted in SAP and are dealt with as part of a scheduled weekly maintenance plan. Such focus means safety concerns are dealt with in a structured and timely manner.
Utilities: As a result of the continued AMIS success and Improvements made to plant reliability and efficiencies, huge strides have been taken in reducing utility costs. Gas, electricity and water use have all decreased by almost 40% and CO2 is no longer purchased for the site.
Waste: Ongoing CI work which has been facilitated by AMIS, includes the installation of the swing sieve, focus on the fermentation and brewing process’s ‘shooting line’ (particles left in the bowl during the centrifuge run are removed by ‘shooting’ every 17min, or earlier if required) and efficient centrifuge runs to reduce loss and improve recovery of beer into the storage vessel. The reduction in waste has improved dramatically. The original waste figures were regularly over 20% waste is now just 7 to 8%. This has had huge fiscal rewards for the site, with every percentage of waste costing a significant amount due not only to wasted materials, but disposal costs too.
Ian Hamilton, St. Francis Abbey Brewery Operations Manager, concluded:
“The asset care benefits for SFAB and Diageo have been remarkable. Cost reductions, reliability, enhanced service and a safer environment have all been greatly enhanced by AMIS. What really impresses me however, is how the teams themselves have really taken ownership for continuous improvement. It has been a privilege to see the growth and development of so many people.”